A Legacy of Quality, A Future of Innovation
With a deep-rooted legacy in the concrete industry, Modern Concrete & Materials was founded in 2019 in Southeast Texas by Trent Almond. This was over a decade after his father, Doug Almond, sold Quality Concrete & Materials, which he had established in 1997. Inspired by his family’s background and driven to build a truly modern concrete company, Trent sought to improve quality through technology.
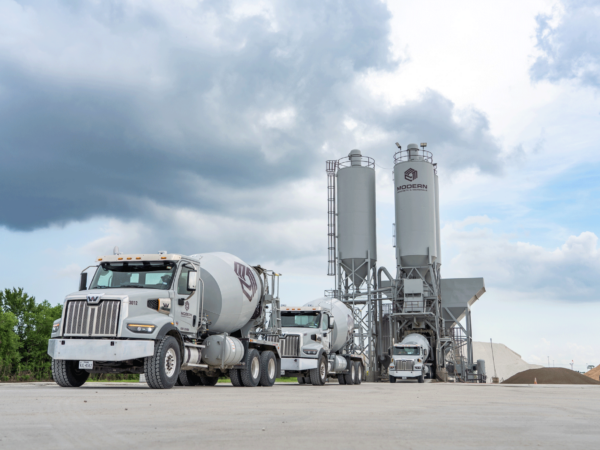
For five years, the company operated without a dedicated concrete quality control software. However, as growth accelerated, so did the need for a single source of truth for all their mix data. With data stored across multiple spreadsheets, compiling and analyzing information became a time-consuming, manual effort. While this approach worked, it made it difficult to consolidate and interpret the data efficiently. Without a centralized system, the quality control team struggled to be as proactive as they wanted, spending more time gathering data than analyzing it.
New Era in Concrete Quality Control
While they initially set out to find a simple concrete quality control solution, the team quickly recognized the potential of Giatec® SmartMix™ — an intuitive concrete quality control system designed to streamline operations and bring data into a single centralized platform. Upon exploring SmartMix’s full capabilities, they understood that investing in a more advanced software would provide far greater long-term benefits. As Trey Lambert, Quality Control Manager, said, “At first, we were just looking to organize our data better, but SmartMix takes it a step further. It brings the optimizations right to us, faster than we could do manually. The potential is huge.”
In only one month, SmartMix helped them transition from manual data entry to a fully automated system, guided by the Giatec Team’s support. Consolidating all their mix, material, and performance-related test data, SmartMix empowered the team to make faster, more strategic decisions. “It wasn’t just about having the data. It was about having it in a way that we could use efficiently,” Trey explained. The seamless integration of SmartMix into their existing workflow made the transition smooth, with minimal disruptions to their operations.
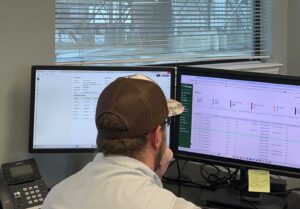
Fast-Tracked Success with SmartMix
The decision to implement SmartMix quickly paid off as Modern Concrete & Materials saw immediate improvements in efficiency. Leveraging the SmartDocs feature, SmartMix automatically uploads their third-party data and sends notifications when issues arise or new optimization opportunities appear. Prior to SmartMix, inputting data from reports would take anywhere from 4-5 days, leaving little to no time for analysis. Now, the process takes just an hour, freeing up almost an entire workweek for more strategic decision-making. Similarly, submittals that previously took 10-15 minutes each can now be generated in just a couple of minutes with a few clicks. Enabling 10x more efficiency in submittal processing, this shift freed up their time to focus on what really matters. “The workflow is what stood out the most,” Trey explained. “It’s simple, fast, and lets us focus on what really matters: optimizing our mixes.”
READ FULL CASE STUDY